Matrice métallique composite (MMC)
Le spectre d'utilisation des composants en métal léger fortement sollicités, principalement en aluminium, mais aussi en magnésium ou en titane, ne cesse de s'élargir.L'utilisation d'alliages légers dans la construction automobile est motivée par la réduction du poids et donc de la consommation de carburant et des émissions polluantes.
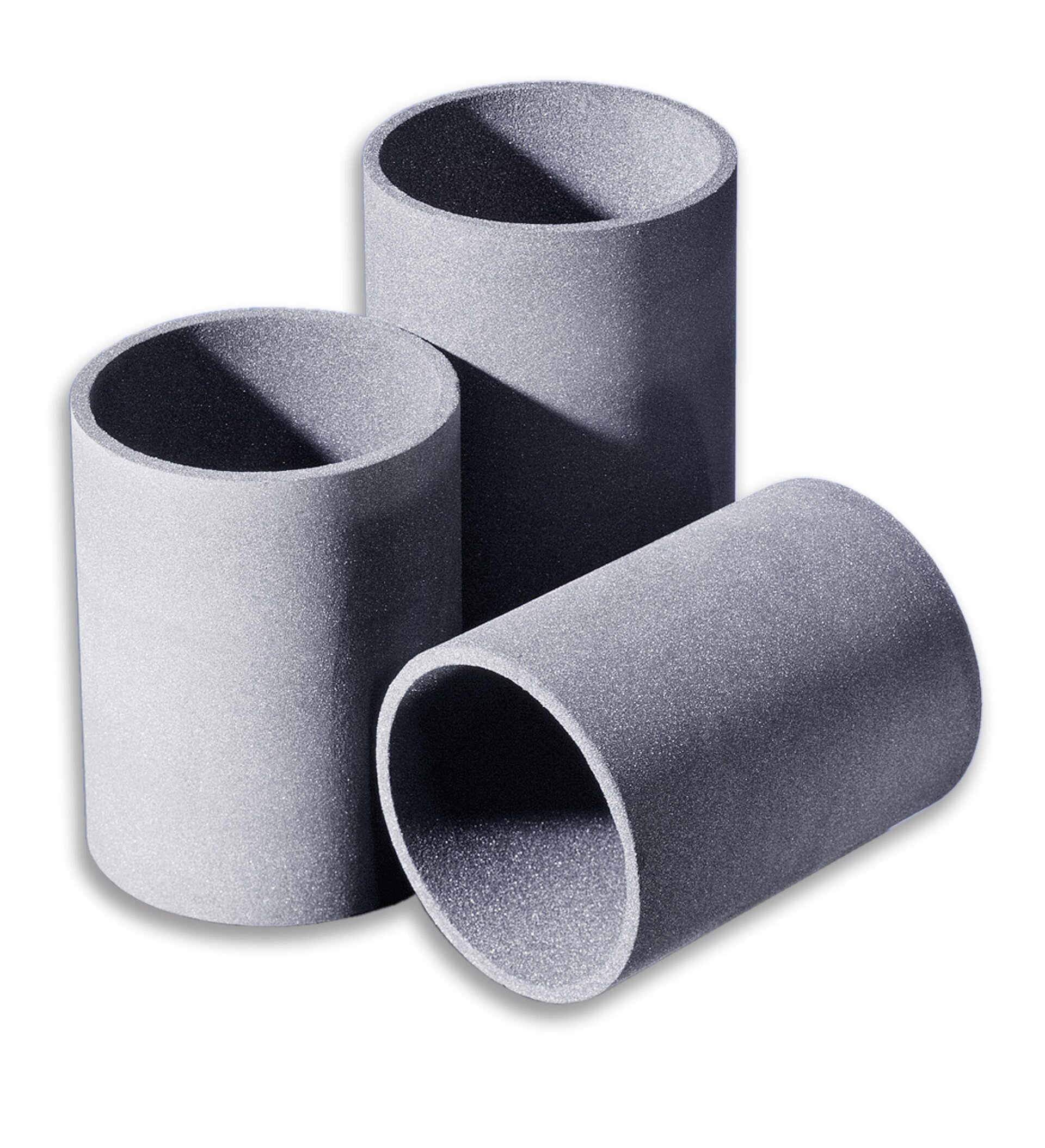
Toutefois, la construction en métal léger atteint ses limites là où elle doit résister à des contraintes tribologiques, mécaniques ou thermiques élevées. La solution consiste à renforcer de manière ciblée les composants légers aux endroits où les contraintes sont maximales. De tels matériaux composites à base de métal et de céramique, appelés composites à matrice métallique (également appelés composites à matrice métallique, MMC), sont constitués d'un métal (matrice) renforcé par des particules de céramique dures.
Le résultat est un produit qui présente les avantages des deux matériaux, à savoir d'une part la légèreté du métal et d'autre part la haute performance de la céramique.
Exemples d'applications des matériaux composites métal-céramique :
- Guide d'ondes d'antenne dans le télescope spatial Hubble
- Satellites commerciaux
- Industrie automobile, par ex. chemises de cylindres et disques de freins
- Aéronautique et aérospatiale, p. ex. manchons de pales de rotor dans les hélicoptères
Les innovations récentes ont permis de réduire considérablement les coûts de production et d'usinage associés aux MMC. En tant qu'entreprise leader dans le domaine de la céramique technique, CeramTec a mis au point un procédé qui permet de fabriquer des composants MMC légers de manière efficace et économique, tout en respectant les normes de qualité les plus strictes.
Les préformes céramiques hautement poreuses de CeramTec sont infiltrées par le métal en fusion pendant la coulée du produit MMC. Il en résulte une transition continue entre les zones renforcées par le métal et celles renforcées par la céramique. Notre technologie des préformes ouvre la voie à une multitude de nouvelles applications.
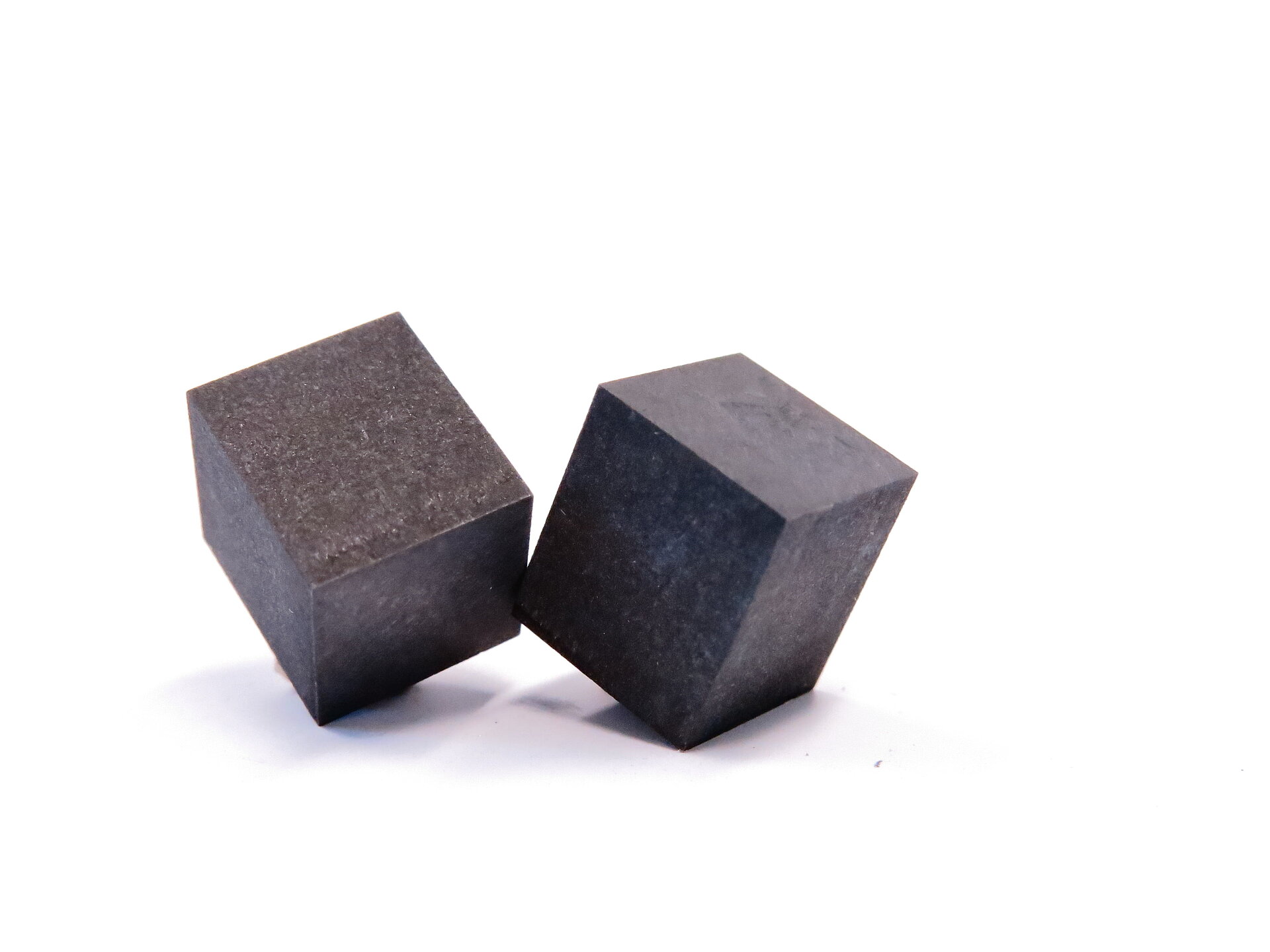
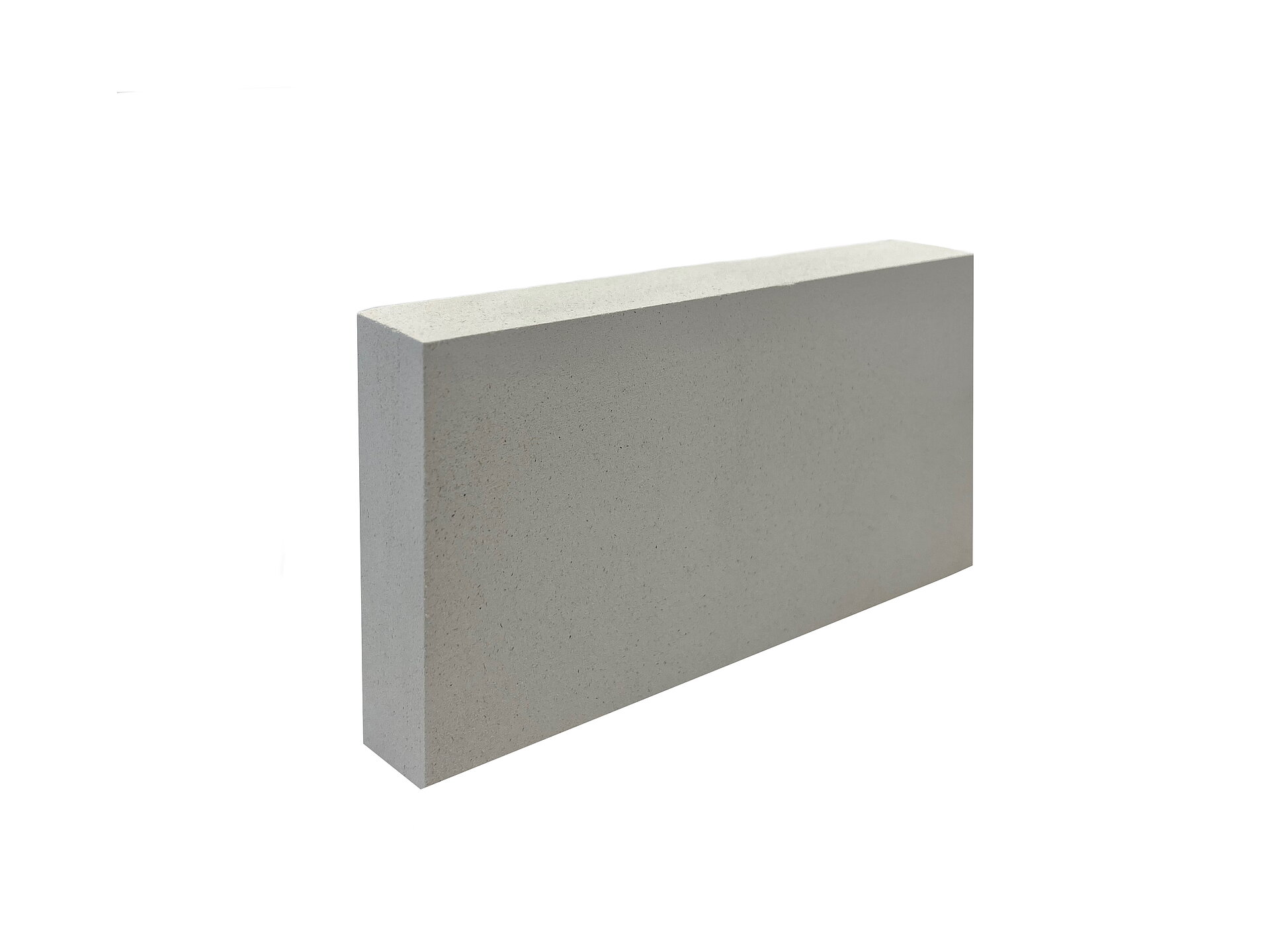
Technologie des préformes
Les préformes MMC de CeramTec sont conçues pour répondre aux besoins de nos clients et peuvent être utilisées avec des alliages d'aluminium standard.
CeramTec propose un pourcentage de céramique compris entre 35 et 70%, les tailles de grains et de pores étant réglables de la même manière. Pour les produits haute performance, un additif de dureté supplémentaire peut être utilisé pour améliorer encore les propriétés. Des géométries variées et complexes sont possibles avec ce procédé de fabrication.
Notre concept de préforme, associé à notre savoir-faire en matière d'outillage, permet d'améliorer les performances et de réduire le coût total de possession. Notre portefeuille de préformes comprend une large gamme de matériaux standard en céramique à base d'oxydes et de non-oxydes.
Préformes en carbure de silicium (SiC)
Une préforme en SiC est parfaitement adaptée à l'optimisation tribologique. L'utilisation d'une préforme SiC offre une meilleure conductivité thermique et une résistance à l'abrasion améliorée. Les disques de frein sont un exemple de composants MMC en carbure de silicium. En raison de leur meilleure résistance à l'abrasion, les disques de frein en MMC génèrent moins d'émissions de poussière de frein, ont une durée de vie nettement plus longue et une réduction de poids d'environ 50 % par rapport aux disques en fonte grise traditionnels.
Préformes en oxyde d'aluminium (Al2O3)
Pour les applications impliquant des composants mécaniques fortement sollicités, un MMC fabriqué à partir d'une préforme en oxyde d'aluminium est un excellent choix. Ce matériau présente une résistance élevée à la flexion, un module d'élasticité accru et une bonne ténacité à la rupture.
Un exemple d'application de MMC en préformes d'alumine est un pont de palier dans un moteur. Le renforcement local de la zone environnante en alliage léger par le MMC permet des constructions plus complexes et un poids plus faible grâce à un module d'élasticité augmenté de 100 % et une résistance accrue de 75 %.
Comme la dilatation thermique du MMC et du matériau environnant sont proches, les contraintes thermiques sont moins importantes par rapport à un pont de roulement standard en fonte grise.
Traitement
L'augmentation de la proportion de particules céramiques dans la préforme MMC peut représenter un défi pour les processus d'usinage dur ultérieurs de nos clients. L'expertise de CeramTec dans l'usinage dur des matériaux céramiques et la fabrication d'outils de coupe en céramique garantit que nous disposons des connaissances nécessaires pour aider nos clients tout au long du processus de fabrication.
CeramTec développe également des outils de coupe pour les MMC et offre des possibilités avec des arêtes de coupe non définies. Nous proposons la découpe au laser pour les exigences de précision élevées et la découpe au jet d'eau pour un taux d'enlèvement plus rapide.
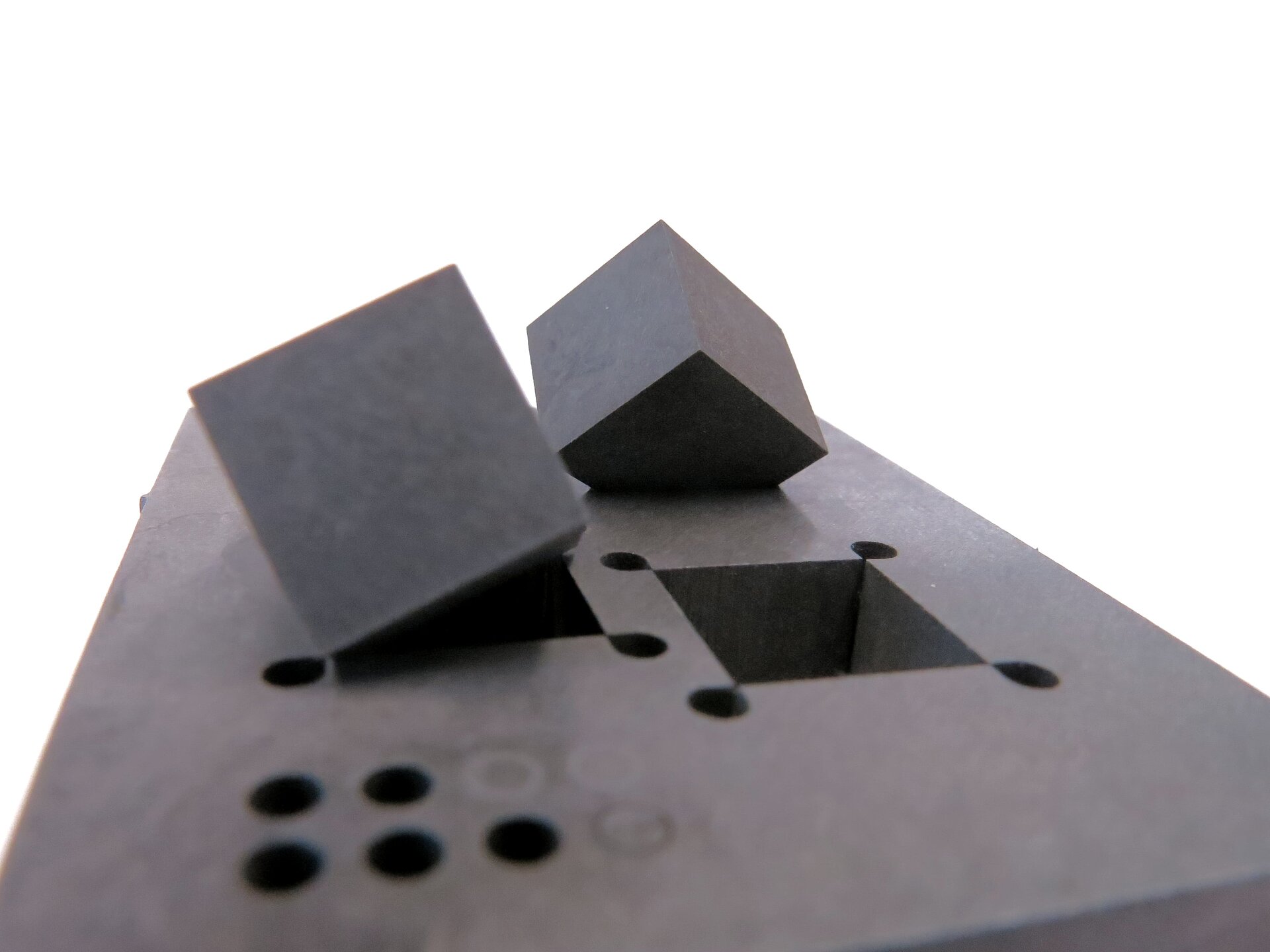